Найважливішим процесом в технології портландцементу є випалення сировинної суміші і отримання клінкеру. В процесі випалення в сировинній суміші відбувається ряд фізичних і физико-хімічних перетворень, в результаті яких утворюється клінкер, що є гранулами чорного кольору, що спеклися діаметром 1-3 см. Мінералогічний склад клінкеру головним чином відрізняється від мінералогічного складу початкових сировинних матеріалів, що обумовлює придбання ним абсолютно нових, заданих нами властивостей. В процесі випалення сировинної суміші відбувається хімічна взаємодія основного оксиду СаО з кислотними оксидами. Спочатку реакції взаємодії відбуваються в твердій фазі, потім при підвищенні температури випалення з'являється рідка фаза і утворення більшої частини клінкерних мінералів відбувається через рідкофазні реакції. Залежно від особливості приготування сировинних сумішей розрізняють чотири способи виробництва портландцементу: мокрий, сухий, напівсухий і комбінований. При мокрому способі сировинні матеріали після їх дроблення тонко подрібнюють в млинах у присутності води, отримуючи текучу сметановидну масу із вмістом води 35-40% - сировинний шлам. При сухому способі виробництва сировинні матеріали висушують, а потім тонко подрібнюють. При мокрому способі виробництва випалення ведуть в довгих печах, що обертаються, при сухому - в коротких обертових печах із запічними теплообмінниками. Напівсухий спосіб відрізняється від сухого тим, що сировинна суміш перед випаленням гранулюється при вологості 10-14%. При комбінованому способі виробництва шлам, приготований за мокрим способом зневоднюють на фільтрах до вологості 16-18% і подають на випалення у печі у вигляді напівсухої маси. Кожен спосіб має свої достоїнства і недоліки. В теперішній час основними способами в світовій цементній промисловості є мокрий і сухий. У всіх країнах клінкер прагнуть отримувати за сухим способом, при якому витрати палива на 30-40% менше, ніж по мокрому і більш високий питомий вихід клінкеру з об'єму печі. У фізичних перетвореннях сировинних шихт, приготованих по мокрому і сухому способам, на початковій стадії випалення є відмінності. При подальшому випаленні, після повного висушування шламу, физико-хімічні перетворення матеріалів відмінностей не мають. При мокрому способі виробництва використовуються довгі печі, що обертаються, в яких відбуваються всі физико-хімічні процеси утворення цементного клінкеру. У печах сухого способу виробництва нагрів сировинної суміші і підготовчі процеси йдуть в циклонних теплообмінниках, остаточна декарбонізація матеріалу і процеси спікання відбуваються в обертовій печі. 2.1 Зміни сировинних компонентів при нагріванні При нагріванні окремі сировинні компоненти зазнають ряд перетворень. Вільний кремнезем, що знаходиться у вигляді β-кварцу при нагріванні переходить в α-кварц, потім в α - тридиміт і α -кристобаліт. Водні гідрати глинозему - гіббсит, байєріт,діаспор при нагріванні зазнають ряд змін з утворенням при 1200 оС α-Аl2O3. Глинисті мінерали - каолініт, галуазит, монтморілоніт - при нагріванні до 50-100 оС втрачають механічно зв’язану воду, від 100 до 300 оС - адсорбційну, при температурах 400-600 оС – основну кількість кристалізаційної води. Безводий залишок розпадається на окремі оксиди, кожен з яких зазнає далі власні поліморфні перетворення. При нагріванні крейди і вапняку в температурному інтервалі 400-600 оС відбувається перетворення арагоніта на кальцит. Дисоціація кальциту починається біля 600 оС. На розкладання 1 кг вапняку витрачається 1780 кДж тепла: СаСО3 → СаО + СО2 - 1780 кДж Дисоціація магнезиту відбувається при температурах 500-700 оС, доломіту - при 600-900 оС. Інтенсивна дисоціація карбонату кальцію йде при температурах 900-1100 оС. У присутності фторидів і хлоридів температура дисоціації знижується на 30-120оС, а швидкість - зростає. Оксиди алюмінію, кремнію і заліза в великих кількостях також прискорюють реакцію дисоціації СаСО3. Аналогічно діють карбонати калію, натрію, хлористий натрій і тріполіфосфат натрію. Дисоціація кальциту є комплексною реакцією. На початковій стадії відбувається розпад іонів СО3 по схемі СО3 → СО2 + О2. Спочатку молекули СО2 адсорбуються твердою фазою, що залишається, з утворенням комплексів (СаСО3)тв → (СаОтв∙ СО2)адс. Потім молекули СО2 десорбуються і покидають решітку кристалу СаСО3 (Рис. 2.1). 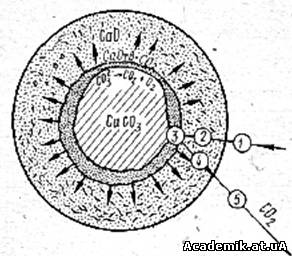 Рисунок 2.1 - Схема дисоціації зерна СаСО3 Кінетика процесу дисоціації СаСО3 визначається швидкістю протікання двох його стадій, освіти зародків кристалів СаО і їх дифузійного зростання. Дисоціація доломіту СаМg(СО3)2 протікає в дві стадії: 1) при 730 оС йде реакція розкладання і дисоціації СаМg(СО3)2 → СаСО3 + МgО + СО2; 2) при 910 оС відбувається дисоціація СаСО3. 2.2 Реакції в твердому стані Всі клінкерні мінерали окрім аліта утворюються в результаті твердофазових взаємодій. Речовини, що містяться в кристалічних гратках сировини Н2О, СО2 при нагріванні матеріалу видаляються. З'являються вакантні місця, що обумовлюють високу активність кристалічних решіток. З підвищенням температури матеріалу відбувається інтенсивний тепловий рух структурних елементів кристалів, яке супроводжується «обміном місць». На початку це приводить до виправлення дефектів будови монокристалів, а потім до взаємодії кристалів різних компонентів один з одним. Результатом цього явища є укрупнення кристалів існуючих фаз і утворення кристалів нових хімічних сполук між ними (Рис. 2.2) Рисунок 2.2 Схематичне зображення процесу. При протіканні твердофазових реакцій найбільш активним («що покриває») компонентом є СаО, а за відсутності оксиду кальцію «покриваючим» компонентом служить більш легкоплавкий. Найбільш поширеною формою рівняння, що описує кінетику твердофазового взаємодії з дифузійним контролем, є рівняння Яндера: , γ - ступінь перетворення «покриваючого» компоненту; -константа, що враховує коефіцієнт дифузії; - тривалість реакції в год. Для реакції клінкероутворення ступінь перетворення визначається кількістю СаО, що ще не зв'язався. При ступені перетворення більше 0,8, коли товщина шару новоутворень зростає і дифузія крізь нього сповільнюється, слід застосовувати рівняння Будникова-Гінстлінга : . Якщо лімітуючою стадією реакції є не тільки дифузія, але і хімічна реакція, найбільш достовірне рівняння Таммана: . У портландцементних сировинних сумішах твердофазні реакції протікають в температурному інтервалі 400-1250 оС; при більш високих температурах з'являється рідка фаза. Унаслідок мікронеоднорідності складу сировинної суміші окремі частинки розплаву з'являються вже при 500-700 оС. При реакціях в твердій фазі відбуваються: дегідратація глинистих мінералів, декарбонізація карбонатів кальцію і магнію, утворення проміжних продуктів взаємодії СаО з кислотними оксидами - СS, C2F, C3S2, C2AS, C5A3 і ін. і формування основної кількості клінкерних мінералів - С2S, С3A, С4AF, і частково С3S. У температурному інтервалі 600-800 оС відбувається утворення С2S, C3S2, C2AS, C5A3, C3MS2 і ін. При температурах 850-1050 оС низькоосновні силікати і алюмінати кальцію насичуються до високоосновніших. Утворюються також проміжні з'єднання CMS, CMS2, C3MS2, C3MS2 і ін. Екзотермічні реакції утворення клінкерних мінералів протікають в інтервалі температур 1050-1250 оС. До моменту появи розплаву в портландцементном клінкері присутні мінерали, що утворилися в результаті твердофазових реакцій C2S, C5A3, C3A, C4AF, 10-15% C3S, периклаз і незв'язаний СаО. При подальшому підвищенні температури в обпалюваному матеріалі з'являється розплав - рідка фаза. 2.3 Реакції, що протікають за участю рідкої фази При температурах більше 1250 оС в обпалюваному матеріалі з'являється рідка фаза в кількості 15-30%. Зовнішньою ознакою жідкофазного спікання є різке зменшення пористості і збільшення щільності клінкеру. Кінцева пористість ромислових клінкерів складає 10-30%. По теорії рідкофазного спікання розрізняють три стадії процесу: 1) перегрупування частинок в результаті їх пластичної течії спільно з рідкою фазою; 2) заповнення пор в результаті реакцій мінералоутворення; 3) рекристалізація з утворенням жорсткого скелета. На першій стадії процесу може бути застосовне кінетичне рівняння У.Кингері: , 1 + х > 1, оскільки розміри пор в процесі спікання зменшуються. Зв'язок між усадкою і η, l, r i τ виражається рівнянням: σ - поверхневе натягнення; η - в'язкість; l - початкова довжина тіла; r - радіус частинок; τ - час. Аналіз рівнянь показує, що інтенсифікувати процес рідкофазного спікання можна зниженням в'язкості розплаву і зменшенням розміру твердих частинок, збільшенням кількості рідкої фази і підвищенням коефіцієнта дифузії. Кількість рідкої фази. Температурний мінімум при якому утворюється рідка фаза за даними Гансена складає: С3S - С2S - С3A - 1455 оС С3S - С2S - С3A - Na2О 1430 оС С3S - С2S - С3A - Fe2О3 1340 оС С3S - С2S - С3A - MgO 1375 оС С3S - С2S - С3A - Fe2O3 - MgO 1300 оС С3S - С2S - С3A - Na2O - Fe2O3 - MgO 1280 оС Подальше пониження температури утворення евтектичного розплаву відбувається лише в незначній ступені, незалежно від видів домішок до сировини, і незалежно від складу спікання реальних сировинних сумішей цементного виробництва, і починається при температурах 1260-1280 оС. По зменшенню флюсуючої дії оксиди можна ровмістити у наступний ряд: Fe2О3 → Al2О3 → MgO У реальних сумішах в період спікання спочатку утворюється розплав внаслідок появи легкоплавких евтектик між алюмінатами, алюмоферитами і другорядними оксидами. При 1400 оС алюмінати і ферити розплавляються повністю і алюмоферитний розплав розчиняє деяку кількість С2S і вільний СаО. Кількість розплаву, що утворився, залежить: від вмісту в суміші Al2О3, Fe2О3, MgO і лугів, співвідношення між Al2О3 і Fe2O3, оскільки це співвідношення визначає, які з'єднання виділяються: С3А, С4AF або С2F, а також від температури розплаву. Кількість рідкої фази для чотирьохкомпонентної системи з різними величинами глиноземного модуля і температури можна приблизно розрахувати по формулах: р < 1,38 р > 1,38 Температура оС: 1338mж= 6,1Fe2O3+MgO+R2O; mж= 8,5Al2O3-5,22Fe2O3+MgO+R2O; 1400 mж=2,95Al2O3+2,20Fe2O3+MgO+R2O; 1450 mж=3,00Al2O3+2,25Fe2O3+MgO+R2O; Залежно від складу сировинної суміші кількість рідкої фази може коливатися від 15 до 30%, але частіше складає 20-30%. Кількість розплаву помітно збільшується при температурі біля 1400 оС, коли повністю розплавляються Al2O3 і Fe2O3. Підвищення температури до 1450 оС сприяє зростанню розплаву лише на 1-2%. Проте для в'язкості розплаву і створення кращих умов для кристалізації необхідно довести температуру до 1450 оС. Будова розплаву. Рідка фаза портландцементного клінкеру в інтервалі температур від 1400 до 1500 оС не є істинним розчином. Вона є структурованою рідиною оскільки містить деяку кількість агрегатів (кристалів сіботаксичних груп і тому подібне), присутність яких обумовлена хімічною природою розплаву. Каркасна структура розплаву складається з кремнекислородних радикалів [SiO4]4- , іонів Ca2+, Al3+ і Fe3+ . Іони Al3+ і Fe3+ існують у вигляді комплексів в четверній [MeO4]5- або шестерній [MeO6]9- - координації. У четверній координації вони проявляють кислотні, а в шестерній - основні властивості. Зв'язок Ме = О значно сильніше при четверній координації, тому комплекс [MeO4]5- переміщується в розплаві в недисоційованому вигляді, а комплекс [MeO6]9- - диссоціює на Ме3+ і 6О2- , які мають високу рухливість. У розплаві існує кислотно-основна рівновага між різними координаційними формами амфотерних елементів. При збільшенні вмісту лужних і лужноземельних елементів в розплаві збільшується кількість малорухливих комплексів [MeO4]5- і збільшується в'язкість розплаву, при цьому знижується коефіцієнт дифузії, сповільнюється процес масопереносу. При збільшенні кількості р- елементів (S, P, B, F, Cl) відбувається дисоціація частини комплексів [MeO4]5- , в'язкість розплаву знижується, інтенсифікується масопереніс і підвищується коефіцієнт дифузії. Процеси розчинення і кристалізації. При розчиненні дрібних кристалів СаО і С2S і інших мінералів в рідкій фазі на їх поверхні утворюється адсорбційний (прикордонний) шар рідини, насичений по відношенню до оксидів, що розчиняються. Швидкість подальшого розчинення кристала залежить від швидкості відведення з адсорбційного шару розплаву іонів, що поступають в нього з кристала, тобто швидкість розчинення кристала визначається: 1) кінетикою хімічної взаємодії розплаву з кристалом на поверхні розділу цих фаз з переходом структурних елементів кристала в прикордонний шар; 2) кінетикою дифузії іонів, що перейшли в розплав, в прикордонному шарі – швидкістю відведення іонів від кристала, що розчиняється. Швидкість розчинення щільних частинок СaО і С2S задовільно описується рівнянням Нернста: dm/dτ = D ∙ (C – C0)/S, m - маса кристала; τ - час переходу; D - коефіцієнт дифузії; S - товщина прикордонного шару розплаву; А - площа поверхні кристала; C0, С- концентрації компоненту в основному і насиченому розплавах. Швидкість розчинення частинок СaО в клінкерному розплаві склала 7,2∙10-6 см/с, а частинок C2S – 2,36∙10-6 см/с, тобто швидкість розчинення СaО в 3-4 рази перевищує швидкість розчинення C2S. При зниженні в'язкості розплаву швидкість розчинення зростає. У присутності Na+ і K+ швидкість розчинення зростала в кілька разів. У розплавах, K2SO4, що містять, або Na2SO4 швидкість розчинення C2S в 3-5 разів перевищувала швидкість розчинення СaО. Інтенсивніше розчинення С2S по порівнянню з СaО спостерігалося також і в розплавах одночасно МgO, що містять, Na2O або K2O. Швидкість розчинення частинок знижується із зменшенням їх розмірів. Таким чином, в розплаві відбувається розчинення СaО і C2S, їх взаємодія з утворенням C2S, а потім кристалізація аліта. Процес кристалізації розплаву з виділенням C3S проходить послідовно три основних стадії: 1) пересичення рідкої фази відповідними оксидами; 2) утворення центрів кристалізації; 3) зростання кристалів. При отриманні клінкеру в інтервалі температур від 1450 до 15000С основною фазою, що кристалізується в розплаві є трьохкальцієвий силікат. Переважне виділення C3S відбувається до тих пір, поки розплав залишається перенасиченим по відношенню до СaО. Із зменшенням вільного СаО починається перекристалізація через рідку фазу недосконалих кристалів С2S і МgO. Кристалізація C3S і С6AхFy починається нижче 13500С. У цей період можливо виділення невеликих кількостей нерівноважних фаз: С5A3, С2AS, 3CaO ∙ 3Al2O3 ∙ CaSO4, NC8A3. Кристалізація евтектики при низьких температурах супроводжується виділенням 3-5% дрібнокристалічних C3S і C2S. Залишкова кількість рідкої фази, що не встигла закристалізовуватися, може утворювати скло. Кристали C3S, що утворилися при рідинному спіканні мають правильнішу форму, ніж що виникли при твердофазових реакціях. У обертальній печі, тривалість рідинного спікання складає 20-35 хвилин. Оскільки аліт утворюється в основному у рідкій фазі, в якій містяться багато інших елементів, в його кристалічну решітку входять іони Al3+ , Mg+2, K+, Na+. У кристали аліта іноді вкраплені зерна беліта і вільного СаО. В результаті усадки при рідкофазному спіканні формуються гранули клінкеру, що мають пористість 17-32%. Зразковий розподіл пор по розмірах, мкм: більше 10-30 - 55%; 1-10 - 15-30%; 0,1-2 - 6-18%; 0,004-0,1 - 15-35%. Кристали мінералу C3S розміром 10-60 мкм в розрізі мають форму гексагональних пластин, а кристали C2S розміром 10-100 мкм - округлу форму. Найбільш сприятливими для роботи печей є клінкери, що містять 23-28% рідкої фази. Вони мають дрібну рівномірну гранулометрію, сприяють утворенню стійкої обмазки. Клінкери, що містять 15-20% рідкої фази, вимагають вищої температури випалення, важко утворюють обмазку, знижують продуктивність печей. Клінкери з високим вмістом рідкої фази, утворюють свари у печі. На стадії охолодження в гранулах, що спеклися, протікають процеси, що роблять значний вплив на властивості клінкеру і цементу. З розплаву першими викристалізовуються C3S і C2S, а алюмінати і алюмоферити, як більш легкоплавкі, кристалізуються при нижчій температурі. При одному і тому ж хімічному складі клінкер може мати різний фазовий склад. За даними Ф.М. Ли і Т. Паркера, залежність мінералогічного складу клінкеру від швидкості охолоджування, характеризується величинами приведеними в табл. 2.1. Швидкість охолоджування впливає не тільки на мінералогічний склад, але і на структуру клінкеру. При швидкому охолоджуванні утворюються дрібні кристали з чіткими гранями. Найбільш сприятливий рівномірний розподіл мінералів, бажано щоб аліт кристалізувався у вигляді витягнутих в довжину кристалів. При повільному охолоджуванні клінкеру можуть виникнути небажані явища: 1) кристалізація MgO у вигляді периклазу, що може спричинити нерівномірність зміни об'єму; 2) частковий перехід C2S в γ - C2S, що обумовлює зниження гідравлічної активності; 3) часткове розкладання аліта. Цементи з повільно-охолоджених клінкерів при високому КН характеризуються помилковим схоплюванням і низькою початковою міцністю. 2.4 Вплив різних технологічних чинників на процеси випалення клінкеру На процеси, що протікають при випаленні сировинних сумішей впливають як свідомо властиві сировині властивості (хімічний і мінералогічний склад сировини, температурний інтервал плавлення, вигляд і кількість домішок і ін.), так і ряд змінних параметрів тих, що не менш істотно позначаються на ефективності трансформації сировина - клінкер, але що піддаються регулюванню (коефіцієнт насичення і модульні характеристики, дисперсність і гранулометрія, швидкість і температура нагріву і так далі). Ступінь впливу перерахованих чинників на кінетику процесу клінкероутворення розглядається нижче. Вплив хімічного складу сировинних сумішей. Збільшення швидкості росту міцності цементу може бути досягнуто при отриманні клінкеру з високим вмістом аліта, а в ранні терміни тверднення - і С3А, що можливо при випаленні сировинних сумішей з високим вмістом СаО, тобто з високим КН. Але при високому КН спікаємість клінкеру погіршується. Збільшення силікатного модуля n знижує реакційну здатність сировинної суміші. Між КН і кількістю зв'язаного СаО існує майже прямолінійна залежність (Рис. 2.3). 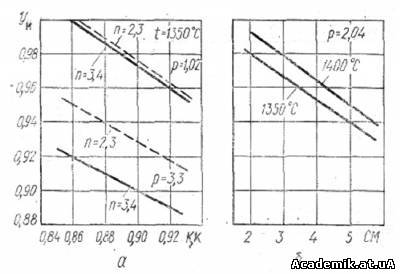 Рисунок 2.3 - Залежність ступеня зв’язаного СаО. Уи від коефіцієнта насичення КН (а) і силікатного модуля СМ (б). Найбільшу реакційну здатність мають сировинні суміші з р = 1,20 - 1,60. Високий силікатний модуль уповільнює реакції силикато-утворення і знижує спікаємість клінкеру, що у свою чергу, погіршує умови охолодження клінкеру в холодильнику, оскільки дрібні зерна, що утворюються, укладаються щільніше і холодне повітря проходить між ними гірше. При виробництві високоміцних і швидкотвердіючих цементів не рекомендується обпалювати клінкер, що містить більше 65-70% аліта і 8% С3А. По різним даним, раціональний склад клінкеру забезпечується при різних значеннях характеристик табл. 2.2. Краща активність клінкерів забезпечується при вмісті силікатних мінералів в межах: С3S + С2S = 75 - 78%, С3S = 54 - 62%, С2S = 14 - 24%. Збільшення вмісту в клінкері аліта вище вказаних меж істотно не підвищує активність цементів. Вплив мінералогічного складу. Реакційна здатність сировинної суміші в першу чергу залежить від природи алюмосилікатного компоненту. Найменш активним є кварц; трохи більшими активностями володіють халцедон і опал. Високотемпературні модифікації ще активніші (тридиміт і кристобаліт), це пояснюється розпушуванням кристалічної решітки при поліморфних перетвореннях. Всі глинисті мінерали високодисперсні і вже тому вельми активні. У інтервалі температур від 400 до 12000С більш високою реакційною здатністю відрізняється субмікрокристалічний монтморилоніт, вельми активні галуазит, гідрослюди, каолініт і відносно менш активні слюда, хлорит, вермикуліт. При температурі вище 12000С відмінність глинистих мінералів по реакційній здатності стає менш значною. Наявність луговмістних мінералів приводить до утворення проміжних з'єднань, які важко розкладаються, що гальмує процес зв’зування СаО. З глинистих порід високу реакційну здатність показують мергель, глинистий сланець, бентоніт і менш активно взаємодіють з СаО лесс, сланець, біотитова глина. Польові шпати мають низьку активність. З карбонатних компонентів найбільш реакційноспроможними є крейда і ракушняк. Дрібнокристалічні вапняки активніші великокристалічних. Суміші, в яких замість СаСО3 вводиться Са(ОН)2, проявляють високу активність, оскільки СаО отриманий з Са(ОН)2, активніше за СаО, що утворився з кальциту. Якщо до складу суміші ввести негашене вапно, то її реакційна здатність падає, оскільки під дією високих температур відбувається рекристалізація. Заміна глинистого компоненту в шихті шлаком приводить до зниженню активності. Ступінь засвоєння СаО в вапняково-шлакових сумішах при низьких температурах незначна. Максимум засвоєння вапна спостерігається в інтервалі температур 1300-14000С. Основні шлаки трохи активніше кислих, оскільки в них вже містяться С2S, С3S2, СS. При швидкому випаленні активність шихти на основі белітового шламу, що містить в основному С2S в гідратованій формі підвищується. При повільному випаленні її активність падаєт в зв'язку з тим, що С2S встигає рекристалізуватися. Не можна говорити про активність алюмосилікатного і вапняного компоненту окремо один від одного. Якщо розпад алюмосилікатного компоненту співпадає за часом з тим моментом, коли швидкість дисоціації СаСО3 вже достатньо висока, то сировинна суміш буде мати найбільшу реакційну здатність. Вплив дисперсності сировинних компонентів. Тонкість помелу суміші істотно впливає на процесиклінкероутворення як на стадії реакцій в твердих фазах так і на стадії рідкофазного спікання. При грубому помолі компонентів деяка частина великих за розміром зерен не встигає повністю прореагувати в процесі випалення і залишається у клінкері у вільному стані. Реакційноспроможними виявляються лише зерна компонентів, що мають розмір менш 100-120 мкм. Особливу увагу слід звертати на тонкість подрібнення кварцу і вапняку, глинисті ж компоненти високодисперсні від природи, їх питома поверхня складає 1-300 м2/г. При великій кількості дрібних частинок в сировинній шихті швидкість зв’зування СаО збільшується (Рис. 2.4). 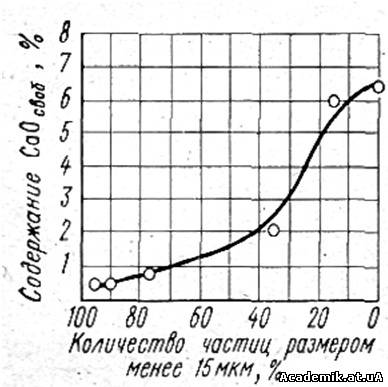 Рисунок 2.4 - Зміна вмісту вільного СаО в клінкері в залежності від вмісту частинок розміром менше 15 мкм в сировинній суміші (1723 К, тривалість випалення 20 хв) Збільшення реакційної здатності дрібніших частинок можна пояснити наступними чинниками: 1) збільшенням поверхневої енергії частинок, за рахунок розриву хімічних зв'язків і зростання частки слабкозв’язаних іонів; 2) відновленням кількості дефектів в кристалах; 3) збільшенням сумарної площі контакту між частинками; 4) зменшенням товщини шару реакції на зернах кислих компонентів; 5) прискоренням розчинення частинок в розплаві; 6) підвищенням ступеня однорідності складу сировинної суміші і можливо, збільшенням щільності укладання частинок. Під дією цих чинників швидкість реакції мінералоутворення змінюється оберненопропорціоно квадрату радіусу зерен. Процесу мінералоутворення при випаленні в найбільшій мірі сприяє помол сировини до розміру частинок не більше 100-120 мкм, при цьому вміст зерен кварцу і кальциту розмірами більше 100 мкм не повинне перевищувати 1 і 6% відповідно. Збільшення дисперсності матеріалу ефективне до певної межі (Ю.М.Дешко і ін.) Підвищення дисперсності частинок від 0-500 мкм до 0-60 мкм підвищує реакційну здатність суміші. Подрібнення сировини до 2-3 мкм погіршує якість клінкеру (М.М. Сичев). Тонкість помелу заводських сировинних сумішей визначається залишком на ситі №008 і складає зазвичай 5-15%. При випаленні у сучасних високопродуктивних печах, тонкість помелу може бути нижче, оскільки тривалість перебування в них матеріалу збільшена, щоб мінерали не встигли рекристалізуватися помел сировинної суміші на таких заводах ведуть до залишку на ситі № 008 20%. При визначенні доцільності тонкості помелу враховується не тільки здатність до спікання сировинної суміші, але і техніко-економічні показники процесу помелу. 2.5 Вплив другорядних домішок Крім чотирьох основних оксидів (СаО, Al2О3, SiО2, Fe2О3) сировинна суміш завжди містить деяку кількість інших елементів, які вносяться з алюмінатним, карбонатним компонентами, з золою палива, переходять з вогнетривів. Деякі сполуки спеціально вводяться в сировинну суміш, як мінералізатори (плавні), що зумовлюють легуючу дію. Особливо зростає кількість другорядних домішок при використанні в якості сировинних матеріалів шлаків, шламів, зол і інших відходів промисловості. Сполуки різних елементів – фосфору, хрому, сірки, марганцю, натрію, калію, барію, фтору, титану та інші домішки можуть робити різносторонній вплив процес зв’язування СаО: 1) прискорювати розпад сировинних компонентів і знижувати температуру протікання цих процесів; 2) змінювати температуру утворення і властивості рідкої фази клінкеру; 3) впливати на процес кристалізації розплаву; 4) модифікувати склад мінералів клінкеру і структуру їх кристалів; 5) підсилювати нерівноважність в системі. Орієнтовні вимоги до гранично допустимого вмісту в сировинній суміші ряду оксидів обумовлені граничним вмістом їх в клінкері табл. 2.3. Ці вимоги відносяться до будь-якої сировинної суміші у якій величина втрат при прожаренні ( п.п.п.) знаходиться в межах 35-36%. При сухому способі виробництва посилюються вимоги до вмісту лугів - 0,5% і хлора - 0,02%. Вплив фторидів. Солі фтороводневої кислоти (CaF2, MgF2, NaF, KF, AlF3, BaF2) і солі кремнефтороводневої кислоти (Na2SiF6, CaSiF6, MgSiF6) і багато інших фторовмістних з'єднань є ефективними каталізаторами процесів клінкероутворення. Фтор є найбільш електронегативним зі всіх елементів. Завдяки цьому фториди впливають на всі види матеріалів. При підвищених температурах їх дія посилюється. Іони F містяться практично у всіх шаруватих силікатах: у гидрослюдах від 0,1 до 0,5, в слюді 0,1- 0,2, в монтморилоніті близько 0,03%. Вапнякові породи містять фтор у вигляді флюориту або фторапатиту. Фторовмістні мінералізатори діють практично на всіх стадіях мінералоутворення. На підготовчій стадії і стадії белітоутворення вони сприяють прискоренню поліморфних перетворень, руйнуванню кристалічної гратки окремих мінералів, прискорюючи протікання реакцій в твердій фазі. На стадії рідкофазного спікання, вони забезпечують появу рідкої фази при нижчих температурах, зменшують в'язкість, збільшують електропровідність, інтенсифікують дифузійні процеси. Активізуюча дія фторидів пояснюється тим, що у присутності водяної пари вони утворюють фтороводневу кислоту, що руйнує гратку SiО2 з виділенням SiF4. Не виключається також і безпосередня реакція між фторидами і SiO2 по схемі: 2MeF2 + SiO2 → 2MeO + SiF4 Підвищена по відношенню до СaО реакційна здатність кварцу досягається при нижчій температурі. Так по даним М.М. Сичева, за 30 хвилин в суміші 2CаO - SiO2 при 11000С кварц зв'язує 10%, а кристобаліт - приблизно 35% вапна. Фториди прискорюють процеси дисоціації СаСО3. У присутності NаF ендотермічний ефект розкладання СаСО3 спостерігається вже при 6900С. При цьому виділяється комплексна сполука СаО ∙ 3NaF, що розпадається при температурі 11000С, що дає активний СаО до моменту найбільш інтенсивного утворення силікатів кальцію. У суміші СаСО3 і Na2SiF6 реакції протікають вже при низьких температурах і практично закінчуються при 600-7000С. Один з найчастіше вживаних мінералізаторов - СаF2, у присутності водяної пари в обертальній печі гідролізуєтся, з утворенням активного СаО і HF, кислота взаємодіє з СаСО3 утворюючи СаF2. Таким чином, відбувається частковий круговорот фтору в суміші. Розкладання глинистих мінералів у присутності фтору наступає при нижчих температурах, відбувається аморфізація продуктів розкладання цих мінералів, виділення кремнієвої кислоти і глинозему у вельми активній формі, що сприяє прискоренню реакцій утворення силікатів, алюмінатів і алюмоферрітов кальцію.. На рентгенограмах сировинних сумішей, що містять 0,5% СаF2, лінії двохкальцієвого силікату виникають вже при 6000С, а при 8000С C2S з'являється значно швидше. У присутності СаF2 при 8500С утворюється комплексне з'єднання спурит 2С2S ∙ Сa2CO3, що розпадається при 9500С на активні СO2, СaО і С2S. С2S і СaО у момент виділення з'єднуються в С3S. Таким чином, спуррит грає роль проміжної фази, яка прискорює виникнення аліта в період твердофазових реакцій. Спурріт вперше був відкритий і ідентифікований доктором технічних наук, професором І.Г.Лугиніной в 1968г. У інтервалі 950-12000С утворюється також фторовмісний аліт складу С19S7 ∙ 2СаF2, що розпадається при 11850С. Проте іноді фторовмісний аліт залишається в клінкері і його слабка гідравлічна активність обумовлює зменшення механічної міцності, що може спостерігатися при вмісті більше 0,5-0,6% фтору. СаF2 також активізує процес утворення алюмінатів. Так, в присутності 1% СаF2 температура появи однокальциевого алюмінату знижується на 800С. В період твердофазових реакцій в присутності мінералізаторів утворюються окремі області мікророзплаву. Рідка фаза з'являється при нижчій температурі. Температура утворення основного евтектичного складу знижується на 80-1500С. Фториди також змінюють фазовий склад цементного клінкеру. У їх присутності трьохкальцієвий алюмінат розкладається на С12A7 і СaО. С12A7 утворює з СаF2 комплексну сполуку С12A(СаF2)х ( де х < 1). На практиці фторовмісні клінкеру містять С3А, С11А7 ∙ СаF2, а також фторовмісні С12A7. З вільного вапна, що виділяється, утворюється додаткова кількість аліта. У рідкій фазі в присутності мінералізаторів розчиняється велика кількість двохкальцієвого силікату і СаО. Розчинення відбувається інтенсивніше, що, у свою чергу, викликає інтенсивнішу кристалізацію аліта. Температура утворення аліта знижується на 150-2000С. Для усунення негативного впливу фтору на механічну міцність цементу вміст фторидів винен бути не більше 0,5-0,6% по фтору. Введення 0,6% плавикового шпату в сировинну суміш дозволяє понизити питому витрату палива на 4% підвищити продуктивність обертових печей, на 4% і міцносні показники цементу на 2,5% МПа. Аналогічні результати досягаються при введенні в шихти 0,2% Na2SiF6. Процес отримання клінкеру інтенсифікується при введенні в шихти 1-3% фторапатиту, близько 10% фосфорфтористого шлаку фтористогипсових і інших фторовмісних відходів. Вплив MgO. Оксид магнію є постійною домішкою вапняків і глин, який входить в їх склад у вигляді доломіту магнезиту, аносеріта, сидеріту; він присутній в шлаках у вигляді диопсида, монтичеліта, окерманіта і може потрапляти в клінкер із хромомагнезитового вогнетриву. Оксид магнію негативно впливає на кінцеві властивості продукту, викликаючи нерівномірність зміни об'єму. Присутність в сировинній суміші силікатів магнію забезпечує отримання клінкеру з дрібнішими кристалами периклазу тоді як наявність карбонату приводить до утворення укрупнених кристалів. При використанні замість глинистого компоненту доменного шлаку периклаз кристалізується також у вигляді рівномірних розподілених зерен розміром від 1 до 7 мкм. Оптимальний вміст MgO в сировинній суміші (до 2-3%) інтенсифікує процес мінералоутворення в результаті збільшення кількості розплаву і зниження його в'язкості. У клінкерних мінералах зв'язується до 2% MgO, залишок виділяється у вигляді самостійної фази - периклазу. До 0,7% загальної кількості MgO може входити в склад аліта, причому більше всього Mg2+ міститься в моноклинному аліті. Вміст MgO в біліті складає 0,25 - 0,35% загального його вмісту. Значна кількість MgO може входити до складу алюмоферитної фази. Чим більше вміст рідкої фази, чим інтенсивніше режим охолоджування тим більше Mg2+ може зв'язатися з алюмоферитами кальцію. Оксид магнію з лугами утворює лужномагнієві сполуки, внаслідок чого негативний вплив надлишку MgO і лугів знижується. Вміст MgO стандартами низки країн обмежений 4-6% згідно вимозі ГОСТ 10178-85 кількість оксиду магнію у портландцементе не повинно перевищувати 5%. Вплив оксиду титану. TiO2 постійно присутній в сировинних сумішах в кількості 0,2-0,5%, входячи в їх склад в виді мінералів рутилу (TiО2 ), ільменіту ( FeО ∙ TiO2), перовскиту (CaО ТiО2), анатазу, брукиту, титаномагнетиту; він входить до складу титанових шлаків. Іон Ti4+ по своїй електронегативності вельми близький до Si4+, тому він досить легко заміщає останній в сполуках. Енергія взаємодії Ti з O2 в розплаві Ti – О більше, ніж в Si - O, що дозволяє іонам Ti4+ деполімеризувати деякі комплекси, викликаючи зменшення в'язкісті розплаву. У присутності 0,1-0,5% TiО2 процеси мінералоутворення значно інтенсифікуються. Оксид TiО2 прискорює процес і знижує температуру дисоціації СаСО3, інтенсифікує твердофазні реакції, знижує температуру і в'язкість рідкої фази. Катіон Ti4+ може заміщати не тільки Si4+ , але і Al3+, Fe3+. Найбільша кількість титану входить до складу алюмофериту, а також беліту. Невеликі кількості титану дають легуючу дію, покращують кристалізацію клінкерних мінералів, підвищують їх гідравлічні властивості. У присутності титану трохи знижується швидкість гідратації і механічна міцність цементу в одно- і дводобовому віці. У подальшому механічна міцність цементів з титановмісних клінкерів до 20% вище, ніж у відсутності титану. Великі кількості TiО2 погіршують процеси мінералоутворення: TiО2 утворює з СаО гідравлічно інертні або малоактивні з'єднання СаО ∙ TiО2 і 3СаО ∙ 2TiO2; знижується також активність беліта і аліта. Вплив оксидів марганцю. Марганець у вигляді MnСО3 (родохрозит) і інших з'єднань присутній у вигляді домішки у глинах, а у вигляді MnS (алабандаїн), MnO2 ∙ SiO2 (тефроїт) і тому подібне - у феромарганцевих шлаках. Оксиди марганцю визначалися спектральним аналізом в клінкерах більшості заводів. Особливо велика їх кількість міститься в клінкерах заводів, що застосовують в якості сировинного компоненту доменні шлаки. Оксиди марганцю (1,5-2 і навіть до 3%), як і оксиди заліза позитивно впливають на процеси мінералоутворення і прискорюють їх. Завдяки значному зниженню в'язкості клінкерного розплаву у присутності оксидів марганцю прискорюються твердофазні реакції (починаючи з 9000С). Марганець має більший, ніж залізо, негативний заряд і здатний заміщати залізо в його сполуках. При цьому утворюються тверді розчини в системі С4AF - C4AM. Вважають, що граничний склад цих твердих розчинів характеризується формулою 4CаO ∙ Al2O3 ∙ (0,4Fe2O3 ∙ 0,6Mn2O3). При використанні доменних шлаків у вигляді сировинного компоненту найбільш сприятливим є вміст рівних кількостей Fe2О3 і Mn2О3 (~ 3%). При значному збільшенні кількості Mn2О3 різко зменшується інтервал плавкості обпалюваного матеріалу, в той же час при використанні легкоспікающихся шихт рекомендується вводити добавки, що коректують Mn2О3, що містять, і що викликають часткову кристалізацію розплаву. Марганець може стабілізувати β - 2СаО ∙ SiO2, розчинність Mn2О3 в β-С2S досягає 4%, а в С3S - всього 0,5%. У присутності оксидів марганцю зменшується кількість вільного MgO, оскільки частина його розчиняється в силікатах і алюмоферитах. При вмісті Mn2О3 більше 4% у печі можуть утв
|